Breadcrumb
3D Printing Over 500 Pieces of PPE for the Nation’s Largest Hospitals
Despite working daily with consumer-level and industrial 3D printers in his roles as a Senior Manufacturing Innovation Engineer and Additive Manufacturing Staff Manager at New Balance, Jason Jammallo, MSEM ’12, never personally owned one. So, in early March, when the coronavirus pandemic shuttered office buildings across the Commonwealth and de-densified cities, Jason bought a 3D printer and brought the fight against COVID-19 into his home. In his one-man operation, Jason has printed over 300 face shields and 250 ear-savers for the nation’s largest hospitals located in Boston.
“I was frustrated that I wasn’t able to do much or affect much change working from home. It felt really strange to be on the sidelines, seeing healthcare workers and other people helping and dedicating so much time, energy and resources to do anything they could,” said Jason. “Knowing that I had been working with 3D printing for over 10 years, I knew I could jump in to actually help.”
Throughout his career, Jason has been working in the innovation space, pushing the boundaries of what domestic manufacturing can be. Whether it’s automation, 3D printing, or something in-between, Jason is no stranger to matching solutions to problems.
According to experts, face shields are shaping to be instrumental in curbing the transmission of COVID-19 from patients to first responders and frontline workers. Reusability has been touted as an important characteristic given stressed face mask supply chains. However, face shields are just one piece of personal protective equipment (PPE) nurses and doctors are finding difficult to source through traditional supply chains. Ear-savers, like the ones Jason is 3D printing, remove the strain of surgical mask elastic bands on the ear.
Jason, who is a member of several online 3D printing communities, is printing PPE that follows publicly available guidelines and is both National Institutes of Health (NIH)-approved and reviewed for clinical and community use.
“Supply chains for critical PPE were drying up and being picked over and I thought that 3D printing would be a great way to jump in and help out, at least until those supply chains catch up,” said Jason. “I’m honestly just using my background and know-how to stand on the shoulders of others who have done a lot of work to design these 3D items and just chip in where I can.”
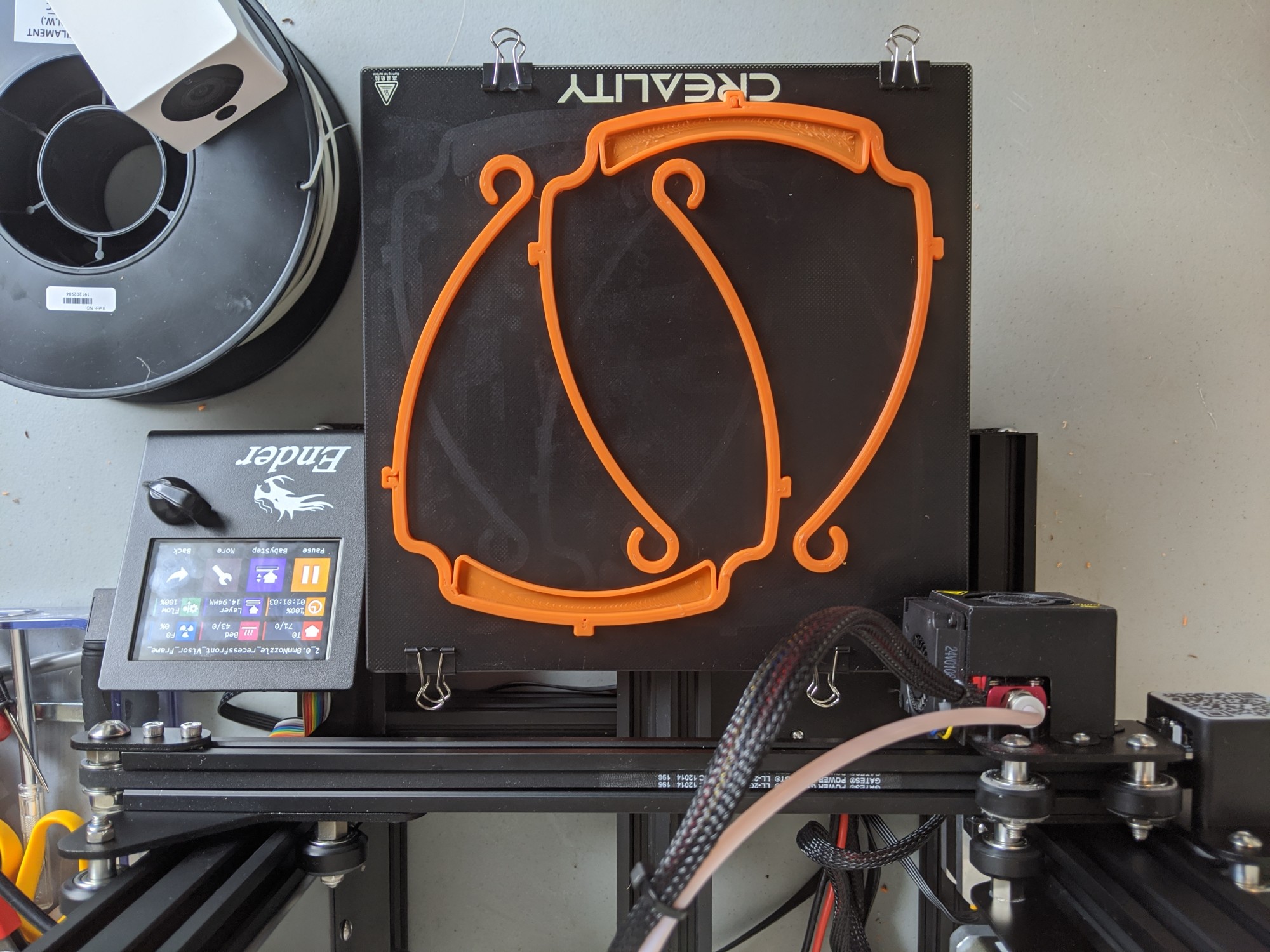
Not long after printing, the PPE would soon make its way into hospitals and word spread beyond professionals in the hospital community. “[The photos of healthcare workers wearing my PPE] were amazing to see. Those few pictures made this time and energy all worth it,” said Jason.
Soon after his PPE got in the hands of medical staff and word got out, Boston-area businesses started reaching out to him to source their own face shields as their businesses planned to start opening back up. In the meantime, Jason has been monitoring news of mass-manufactured PPE resupply in hospitals to better understand when the need for community donated PPE will slow down so he can start to focus on helping local businesses with their PPE needs.
Jason said, “I want to make sure I prioritize these to the right places; healthcare workers and first responders get first priority then come Somerville and surrounding area businesses like hairdressers and restaurants.” Those sales will help to fund materials for future PPE donations to hospitals.
A seasoned innovator, Jason is no stranger to making things with an emphasis on utility. Jason’s small business, Wilhelm Seam, a small-batch leather goods company out of his home in Somerville, Mass., has helped him understand the importance of quality products and backing them with his name.
In a 2016 interview with Scout Somerville, Jason said, “I want Wilhelm Seam to be bigger than what the actual product is.” Although his latest efforts are separate from his traditional products, the intrinsic sentiment has become almost prophetic.
“It’s really important for me to make things that are useful to people and things that people can use every day and enjoy. I get immense satisfaction from building things that are useful,” said Jason.
He added, “I don’t want to put my name on or sign off on anything whether at work or in my personal life that I can’t stand behind.”
Whether it’s through his work with New Balance, Wilhelm Seam, or even 3D printing PPE, the Tufts Gordon Institute alumnus is reminded of the pivotal skills he gained through the MS in Engineering Management program.
“I’ve been using project management-focused courses from the MSEM program every day. That’s certainly helped me with taking on bigger picture projects at New Balance: Becoming a project manager on emerging technology projects, leading different teams for new manufacturing initiatives, and expanding innovation programs,” Jason said.
As Massachusetts, like many other states, begins to reopen amid a new normal, the journey towards eradicating the pandemic-inducing virus continues. But Jason isn’t slowing down yet. “As long as there is a need and as long as I am able to continue printing these, I will continue to print them,” said Jason.